COVID-19: ONE YEAR LATER
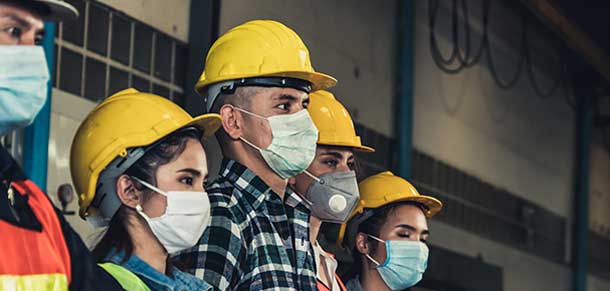
Wearing personal protective equipment and frequent cleaning and sanitizing of machinery became mandatory.
COVID-19 led to more enhanced health and safety measures
The COVID-19 pandemic altered traditional means of doing business, for those who are fortunate enough to still go to work.
Langenburg Redi-Mix, the road construction company that handled the Highway 39 revitalization project in 2020, experienced its share of health risks and challenges over the past several months. Thankfully, all crew members remained healthy and symptom-free for the 2020 working season.
That’s a testament to the company’s approach to health and safety.
“It definitely was a challenge … We did it successfully,” said Kyle Rivett, P. Eng., project manager with the Coco Group, the company overseeing operations. “For that to happen, I think everybody had to be on board with what we were doing. We had to plan ahead for almost everything we were doing … and everybody worked safely.”
Adopting new routines
Road crews routinely were greeted with new work safety protocols which required several updates to safety documentation. Staff needed to be kept up to date on the changes to things like making a note of which visitors were on job sites and the time of day they were present.
As well, more portable washrooms and hand-washing stations were added to job sites.
These changes didn’t have an effect on the road construction efforts.
However, the behind-the-scenes efforts like internal and external communications took on a new approach.
“We’re a very personable company,” Rivett said. “Our staff likes to talk face to face with business owners, reeves and administrators about upcoming work that may affect them. But we had to change those in-person meetings to phone calls and emails. It was more virtual correspondence, which sometimes isn’t as efficient.”
Communication with staff also had a different look.
“We had to address how we did our morning safety meetings,” Rivett said.
“We couldn’t have 100 people standing around in a circle in the mornings. Some people were listening in through radio and we had smaller groups and more open spaces for meetings. We definitely had to change how we relayed information.”
– Kyle Rivett, P.Eng, project manager for Coco Group
name=”separator” style=”height:20px;”>
2020 anything but normal
Allan Goldstone, safety director with the Heavy Construction Safety Association of Saskatchewan, said any hints of normalcy in this industry are far and few between this year.
He and his safety training staff normally train approximately 2,000 people during the winter months. This year, however, has been different thanks to the coronavirus.
“In the 20-plus years I have been with the Safety Association, I’ve never seen it as busy as it was during that first month of COVID-19,” Goldstone said. “With all of the new rules and regulations that were being introduced, contractors didn’t have anything in place that met those requirements. No one did.”
So, instead of teaching and auditing, Goldstone and his team created documents and templates for contractors to corroborate health checks for daily and weekly toolbox meetings.
Goldstone said safety training during the summer months, which they did in 2020, is rare. But it’s the reality they’re faced with during these times of alternative measures.
A big reason why training sessions were still being conducted into June and July was because class sizes had been significantly reduced in order to meet proper physical distancing.
Classrooms shrunk from holding between 20 to 30 students to eight at maximum. As a result, what would normally take one day of training turned into three days of training.
“Unless we were going to rent a ballroom, we were stuck with training eight people at a time because of social distancing guidelines,” Goldstone said. “Either we rented a bigger space to do the bigger classes, which was going to add costs for our association, or we stayed with the classroom we already had and were already paying for and held smaller classes.”
The actual training was altered as well. Goldstone said they were limited to the training they could do because some classes were hands-on.
For example, a confined-space rescue class normally sees at least four people in a group in close contact. The confined-space entry portion of the class remained the same because it was theory only. But the confined-space rescue itself, with one person in a manhole and at least three others peering into the manhole, couldn’t be done.
Thankful for technology
Where in-person training was limited, technology was expanded. Webinars, for the first time, were introduced into safety training classrooms.
Flag person training normally was conducted through in-class teaching. It was available online last year.
“One thing this pandemic has taught us is that we should be looking at all the course material that we have and trying to decide what can actually go online,” Goldstone said. “This has forced us to embrace technology.”
“We’ve never used a Zoom platform before. We had Microsoft Teams, but we’ve never really used it. It has helped us immensely because we’re still able to communicate and collaborate as an association when we’re working on a template.”
Temporary or permanent changes?
The spring and summer months last year, when many businesses across the province were closed, posed a challenge for hungry remote-working road crews. Where would they find their next meal?
Thankfully, rural restaurants stayed open and provided take-out meals for crews. It just required advanced notice to the kitchen staff.
Eating on the job site rather than indoors at a restaurant was a slight change of routine.
Rivett said his crews frequently staged their workdays according to a grocery store’s new hours of operation. They made special arrangements so staff could leave early to pick up food.
Whether these new measures are temporary or become the new normal remains to be seen. Both Rivett and Gladstone and other contractors are taking the wait-and-see approach.
Nonetheless, these alternative means of doing business certainly are better than no business.
“We felt we had to find a way to help the contractors,” Gladstone said. “If we could find a way to do things safely for ourselves and for the contractors, then we were going to do it. We made the decision to move forward and turn this pandemic into a somewhat normal situation.”